業界を知る2023年5月16日
難燃塗料で金属代替・樹脂化を実現する画期的ソリューション
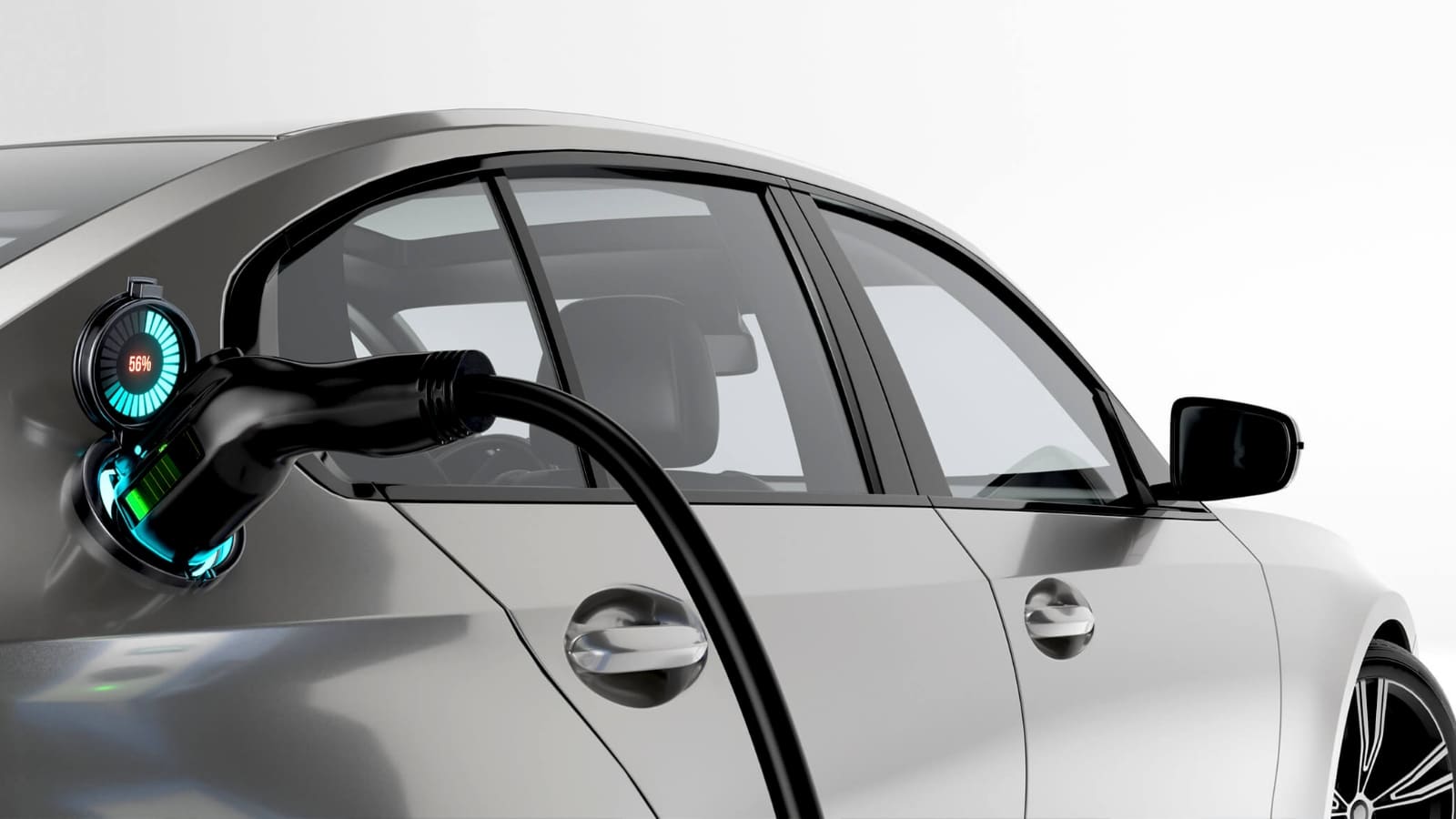
2050年カーボンニュートラル・脱炭素社会の実現に向け、自動車産業に関わる世界中の企業がCO2排出量低減に向けてEV自動車の製造・販売戦略を掲げています。 三井物産プラスチックも、モビリティ事業を通じてEV自動車普及の解決方法を模索するなか、その車両本体の課題である軽量化のテーマについて、「難燃塗料」というソリューションに活路を見出しました。現在進行形で改良を重ねている難燃塗料の開発ストーリーについて、プロジェクトチームのメンバーに話を聞きました。
EV化が加速する時代
私たちだからこそできることを模索
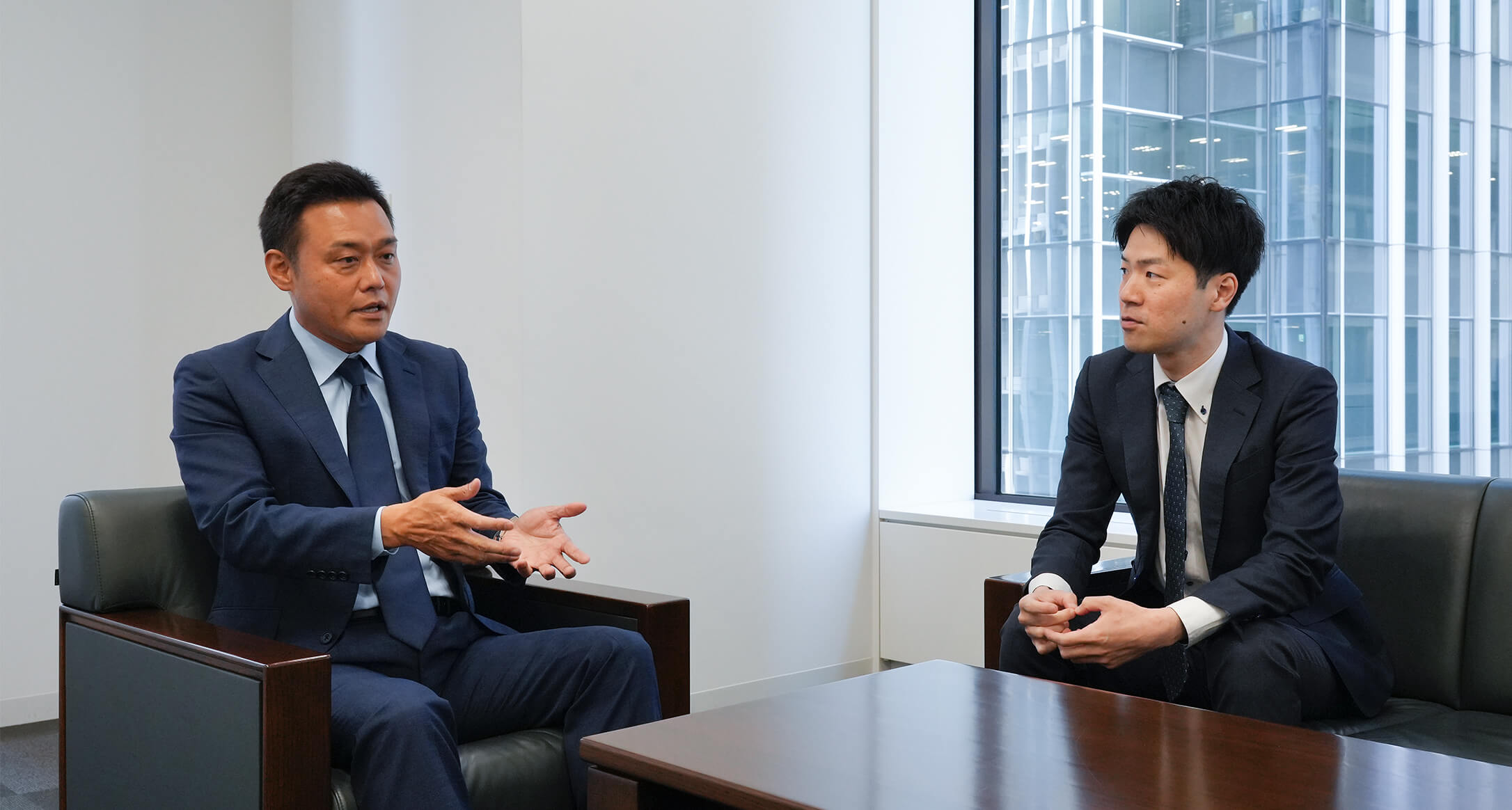
―まずは改めて、なぜ今自動車の金属部品の樹脂化や金属代替、つまり金属に替わる素材が求められるようになったのか、お聞かせください。
戸村:気候変動の問題が深刻化するなかで、世界中で環境保護の意識が高まっています。走行中の自動車による二酸化炭素(CO2)の排出は、温室効果ガスの大きな源の一つであり、EV化はこの問題に対する解決策として注目されています。
竹田:欧州を中心に世界中で脱ガソリン車の動きが活発化するなかで、当初はディーゼル車が先行しましたが、ディーゼル車はCO2や有害物物質等を排出しますから、徐々にハイブリット車やEV自動車が注目され始めました。エンジンとモーターで走るハイブリッド車は、走行段階で化石燃料を消費してCO2を発生させます。一方、電気自動車はバッテリーに蓄えた電力でモーターを回転させて走るため、走行段階では排気ガスを一切出しません。
発電量の約80%が火力電気に頼り切っている日本では、電気の製造過程でゼロエミッションではないという意見もありますが、世界基準で見た場合、現時点ではEV自動車に軍配が上がっているという状況ですね。
戸村:そのような背景から、世界的にEV化が一気に進められるようになったのですが、EV化を進めるうえで大きな課題として浮かび上がったのが、車体の軽量化です。EVは従来のガソリン車と比べて、バッテリーの重量が非常に重くなります。バッテリーは車体の重量の大部分を占めるため、車体の軽量化をしない場合、電力の消費量が増え、充電量が減少し、航続距離(一度の充電で走れる距離)が短くなってしまうのです。さらに、軽量化によってEVの加速性能や運動性能を向上させることもできるので、各社が今まさに競って開発しているというわけです。
―そこで重量のある金属部品をプラスチック化することで、車体を軽量化しようという流れにつながるのですね。
竹田:そうですね。金属を樹脂などで代替すること、いわゆる金属代替・樹脂化ができれば、車体全体がかなり軽量化されるのですが、ご存じの通り、樹脂というのは石油由来のため、金属に比べて燃焼しやすいのです。その課題をいかにクリアするかというのが、軽量化の大きなテーマではないかと考えています。
戸村:樹脂化のテーマが注目されるなかで、専門商社としてプラスチックに関する長年の知見と幅広い取引先ネットワークという資産を持つ当社において、果たして何ができるのか?ということについて、以前から検討されてきました。
竹田:その一環として、2019年4月に「モビリティ事業本部」が発足し、EV化に伴う樹脂の課題に取り組む専門チームが発足しました。このチームで当社ならではのアプローチを様々な面から模索し始めたというわけです。
バッテリーの樹脂化を難燃塗料で解決
信頼できるパートナーと開発スタート
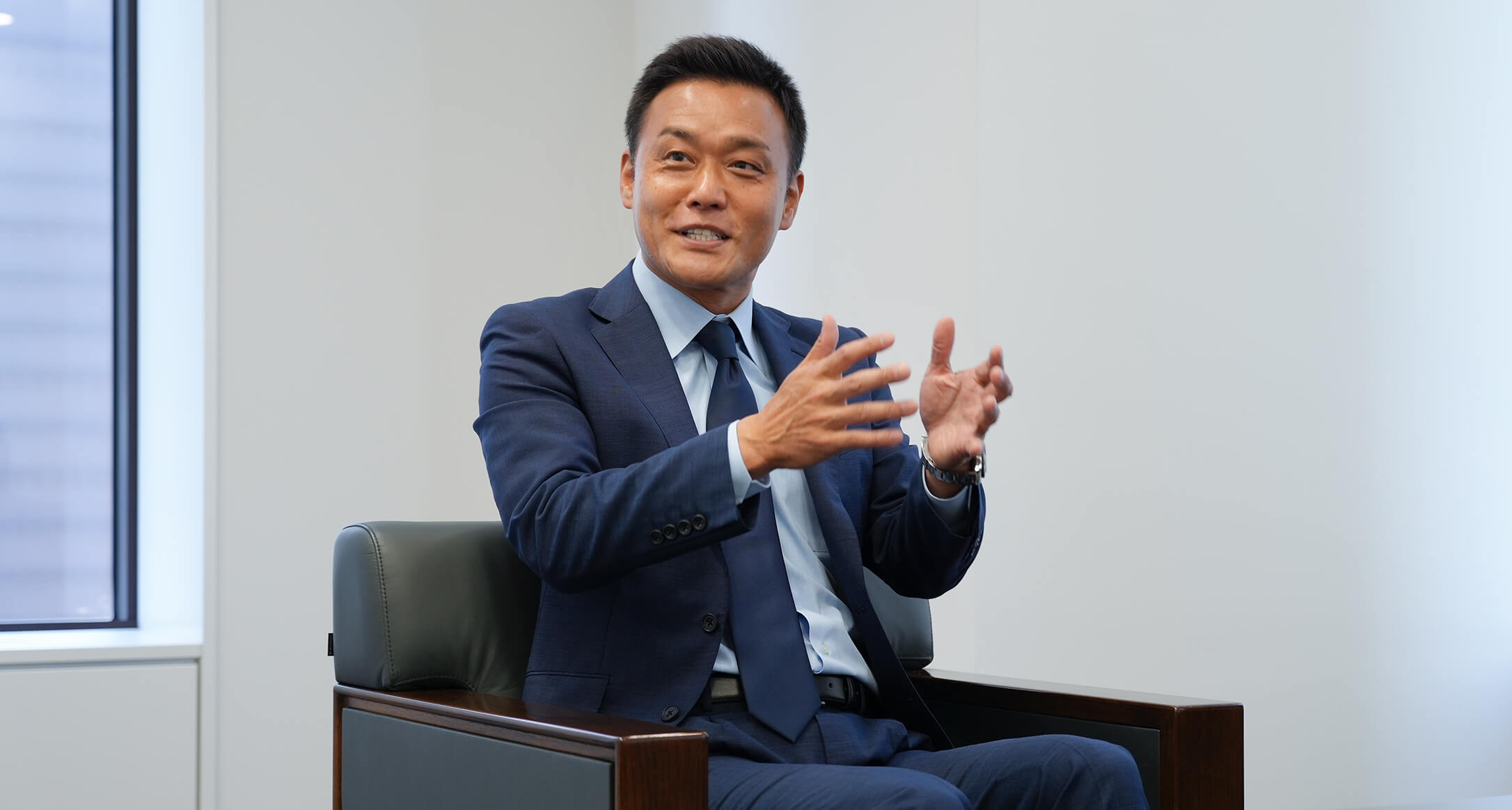
―最初はどのようなところからスタートしたのでしょうか?
竹田:EVの構造はシンプルで、バッテリー、インバーター、モーターの3つが主な要素です。そのなかで、やはり最も重量のあるバッテリーに焦点を絞りました。自動車OEMメーカー様や樹脂加工メーカー様にヒアリングしたところ、バッテリー周辺の樹脂部品は、リチウム電池が燃えたときに高熱に耐える必要があることが課題でしたが、燃焼条件をクリアできる樹脂を開発すれば採用してもらえるだろうということが見えてきたのです。当社の取引先である樹脂メーカー様、加工メーカー様に色々とお声を掛けさせていただき、ご賛同くださった企業と協力し、開発がスタートしました。
戸村:まずは強度や耐熱性の高いエンジニアリングプラスチック、さらにはスーパーエンプラでこの課題をクリアできないかと検討しました。しかし、スーパーエンプラは高価であるため、金属代替としてのコストメリットを出すことが難しく、量産化は厳しいという結論になりました。それから、部分的な金属代替ということで、金属に樹脂を接着させ、樹脂が熱に当たらないようにするという試みもしたのですが、なかなかくっつかないんですね。こちらの方法も断念しました。
竹田:試行錯誤のなかで、樹脂そのものに改良を加えても、これ以上よい結果が得られないだろうというのが見えてきました。そこで次の段階では、塗料に目を付けたのです。比較的加工が簡単であるのと、当社と繋がりのあるパートナーと一緒に取り組みたいという思いがあったので、得意の樹脂と塗料の組み合わせでクリアできないかという発想になったのです。
【関連記事】金属代替・樹脂化の課題は〈難燃塗料〉で解決できる
難燃性レベル5VA以上を達成
現在進行形で改良中
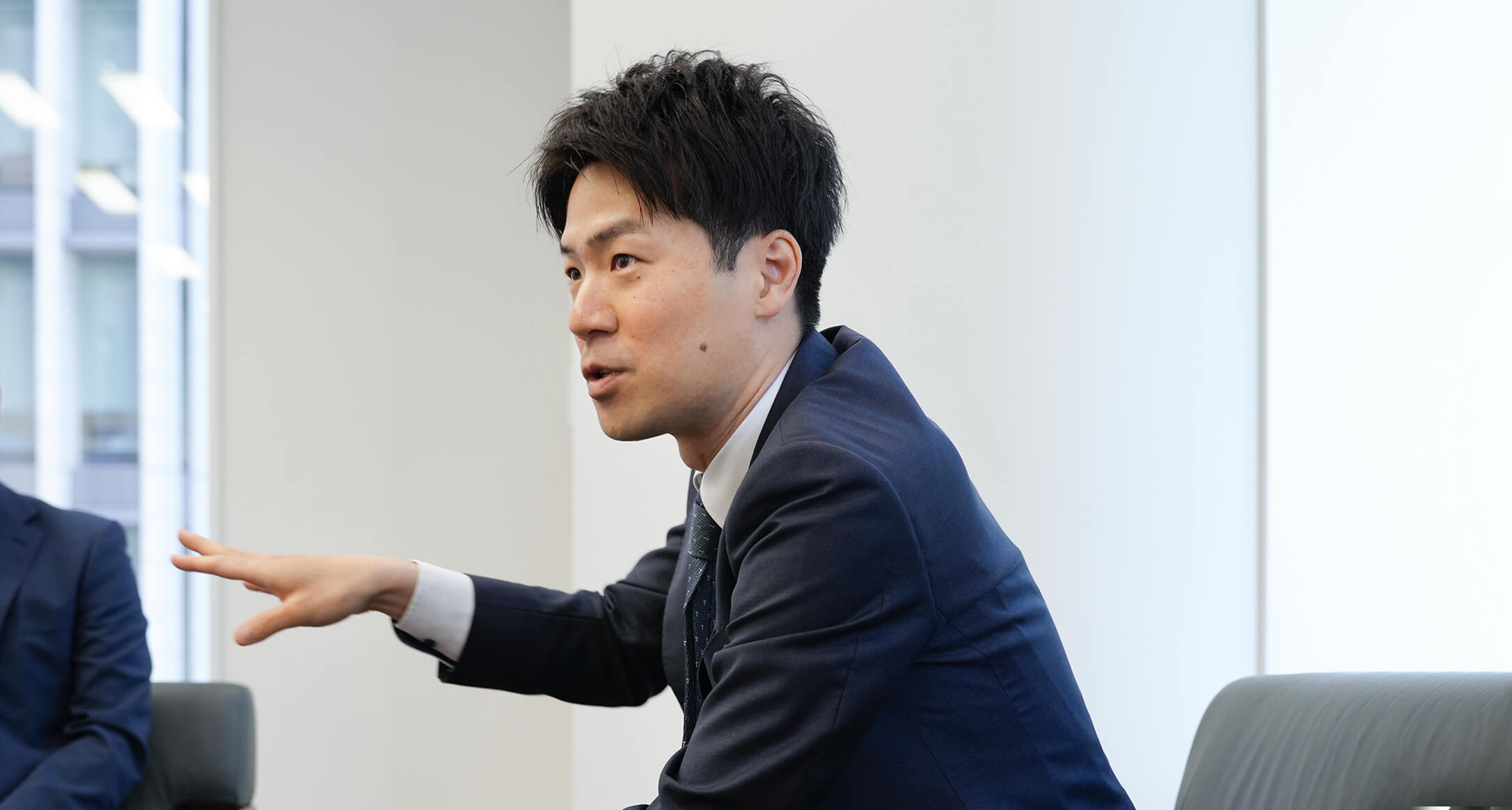
―開発した塗料の特長をお聞かせください。
戸村:まず、軽量化のために金属部品を樹脂化することが必要なのですが、燃えにくい樹脂部品というのは肉厚であることが必須になります。薄くしてしまうと樹脂の持つ難燃性を活かしきれず可燃性が高まるためです。しかし、肉厚の樹脂では、形状の複雑な部品に加工することが難しいのです。そこで、樹脂はなるべく薄くし、自由に形状を加工できることを担保したうえで、難燃塗料を塗布する形にしました。
竹田:パートナーである塗料メーカー様と共同開発したのですが、自動車部品向けの難燃塗料というのは塗料メーカー様にとっても初めての取り組みでした。これまで自動車業界においては、難燃性という考え自体がほとんど重視されてこなかったためです。完成品を用いた実験では、燃焼グレードでは最高レベルの「5VA」以上の難燃特性へと引き上げることに成功しました。
戸村:さらに当社の取扱量が多いエンプラと組み合わせることで、1,000℃の炎で5分間連続加熱しても耐えられることを実証できました。これは非常に画期的なことです。
竹田:実は安全性の統一規格である「UL認証規格」に照らすと、それをクリアする水準の塗料は割と早い段階でできていました。しかし、自動車OEMメーカー様に相談したところ、その水準では満足できないと言われたのです。例えば、UL規格では炎に5秒間耐えられればよいところを、自動車OEMメーカー様の規格では、直火で5分間になる等、かなり高水準での結果が求められています。自動車OEMメーカー様でも今までなかった規格を試行錯誤のなかで新しく作っていっているわけですから、5分間の燃焼実験をクリアしても、さらに高い水準を目指せないかと実証実験を繰り返すのです。さらなる性能向上を目指し、現在もこの難燃塗料は改良を重ねているところです。
―開発した塗料の特長をお聞かせください。
戸村:難燃塗料については、すでに当社が特許を取得しております。自動車をはじめ、世界中の製造業で大きな流れとなっている金属代替・樹脂化・プラスチック化に当社ならではの貢献ができると考えています。海外だと欧米等でも難燃塗料の開発が注目され始めているという話も聞くので、我々の進む方向は間違っていないと確信しています。
それから、最近では自動車以外の用途としても引き合いをいただくようになりました。高度な機械類や、鉄道、医療関係など、耐熱・難燃要求が高い分野の方々が関心を持ってくださっており、我々が貢献できる範囲は非常に広いと感じています。
竹田:このような新しい試みは、身近なパートナーとでないとスピード感をもって進められないんですね。そういう意味では、モビリティ事業本部の立ち上げから約半年である程度のレベルの塗料ができたのは、パートナーの皆様のおかげです。新しい試みは腰が引けてなかなか進められないケースも多いなかで、我々の考えに賛同いただいて、燃焼試験の設備を提供してくださる企業様もあり、当社がこれまで長年築いてきた取引先様とのネットワークがあってこその取り組みであると感じています。
パートナーと共に新たな価値を生み出し、形にしていくという、商社ならではのアプローチで、これからも国内自動車産業の発展に貢献していきたいと考えています。
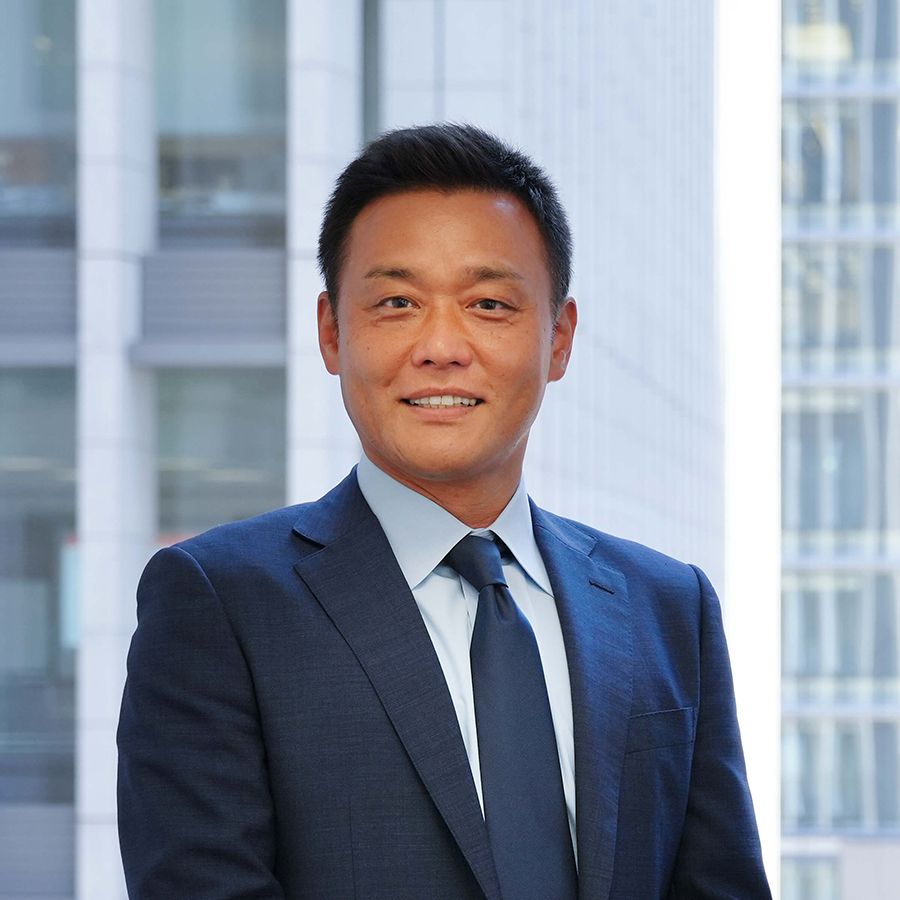
竹田 信也
三井物産プラスチック株式会社 モビリティ事業本部 本部長補佐
入社以来、合成樹脂や製品販売を担当し、現在では自動車分野での新規事業開発に従事。
モビリティ素材ユニット シニアユニット長を経て、現職。
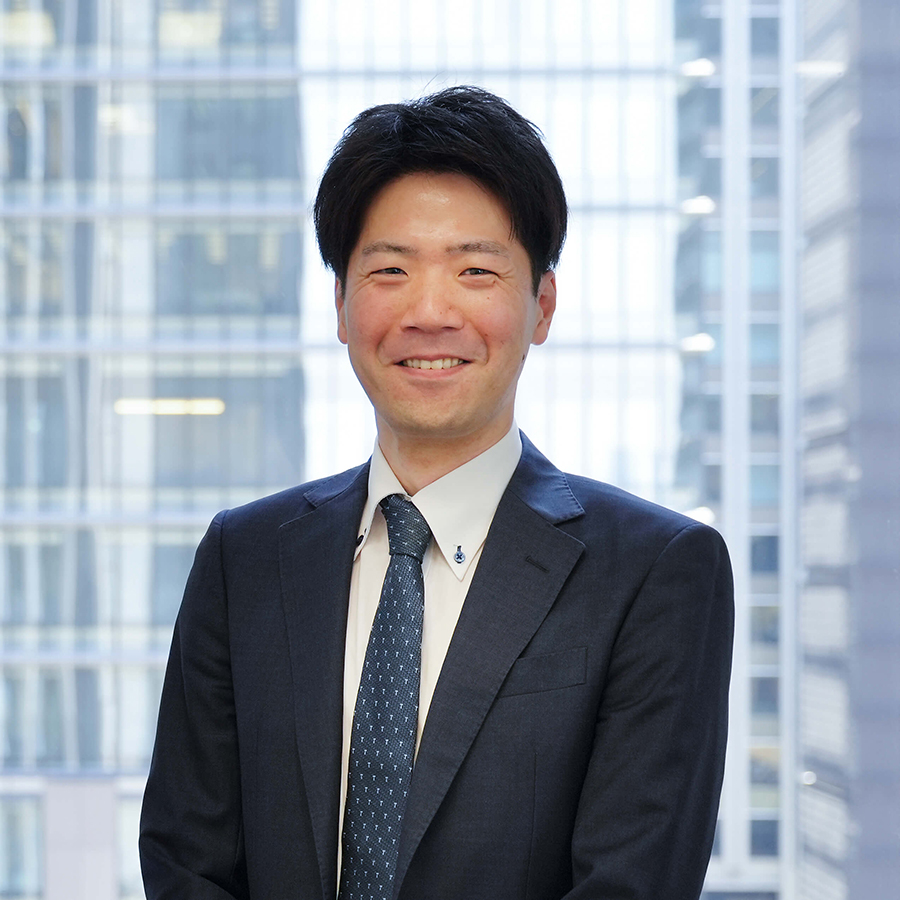
戸村 翔
三井物産プラスチック株式会社 モビリティ事業本部 モビリティ素材ユニット
自動車業界向けを中心にエンプラ販売に従事。
金属代替・樹脂化をキーワードに難燃塗料の開発・市場展開プロジェクトをリーダーとして牽引。